
FAILURE ANALYSIS
To advise whether to run, repair, replace or upgrade, the evaluation starts with a CAD model of critical design features. It proceeds by simulating the structure's response to the mechanical and aerothermal loads within the operating cycle. For turbo-machinery this involves the forces imposed at start-up, base load operation, load following, variable speed operation or daily cycling.
SERVICES
Failure analysis brings multiple disciplines together to form a cohesive explanation as to why cracks formed prematurely or rupture occurred. Results are used to manage and optimize the timing for planned maintenance based on the calculated risk of a catastrophic failure.

Structural (FEA) or flow (CFD) modeling is applied to explain which steady, dynamic or thermal stresses are responsible for damage found on cracked, eroded or corroded surfaces.
Fracture mechanics and fatigue life analysis complete the story, by correlating the rate of damage caused by operating stresses against the record of service prior to when crack or fracture was discovered.
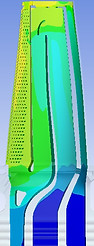

DESIGN EVALUATION

Where a proposed modification is meant to correct a design issue, a comparison is made not just of stress, but also the damage tolerance or projected fatigue life of an original part in order to qualify how well the corrective changes will work.
DAMAGE TOLERANCE

Failures of large turbine or compressor blades were often associated with high cycle fatigue (HCF) due to bladed-disk vibration. Where vibration may be the root cause of premature cracking or fracture, blade frequency margins against resonance are used to distinguish synchronous from non-synchronous problems. Campbell and interference diagrams show the effects of stress stiffening with increasing rotor speed and disk flexibility on frequencies for different nodal diameter modes. Dynamic stress patterns are used to identify the vibrating mode involved. Tip displacements calibrate blade vibration measurements in terms of stress and fatigue anywhere in the blade.
Depending on characteristics of the structure (frequency, stress distribution) and operating environment the appropriate fatigue, fracture mechanics or creep models are selected to predict the remaining cycle life of new or damaged components and identify when they should be inspected.
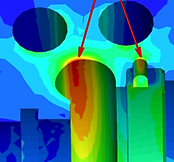
RISK ASSESSMENT

Not all damage presents an imminent threat of failure. Life prediction is used to assess how long damage found at an inspection can be tolerated, or if limited measures to remove erosion, pitting or small cracks may be applied to safely avoid unscheduled maintenance outages.
