
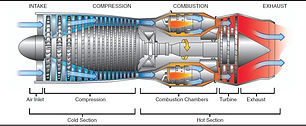
GAS TURBINE
Higher firing temperatures have required gas turbine blades to adopt more complex cooling schemes, directional solidified/single crystal alloys and the application of thermal barrier coatings. Scaling up earlier designs imposes unforeseen localized higher stresses, accelerating damage caused by oxidation, thermal-mechanical fatigue (TMF) and creep, particularly for the first stage blades and nozzles. Also, issues of shroud lifting and cracking associated with creep become more prominent for later stage blades due to increasing radius and operating temperature.
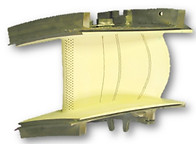
To simulate hot gas path components, a conjugate modeling approach (FEA+CFD) is best suited to analyze such a complex system, where internal cooling, external heating from the hot gas path, heat conduction and structural response of the blade or vane are solved simultaneously to predict the temperatures and stresses throughout the system.





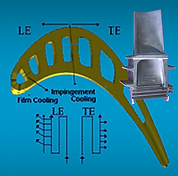
TTI's gas turbine work has been focusing on design evaluations and modification assessments on gas turbine units supplied by major OEMs (Siemens, Mitsubishi and GE) and third party suppliers in the areas of:
-
Aerothermal calculations of gas turbine flow/heat transfer (both hot gas path and cooling flows) and metal temperatures.
-
Prediction of coating oxidation life.
-
Stress calculation and thermal mechanical fatigue (TMF) life assessment.
-
Stress relaxation calculation and creep life assessment
