Case study: SCC Damage Tolerance Assessment of L-1 Blades
Stage: L-1 stage in a LP steam turbine
Issue: Suction side SCC cracks observed for L-1 blades during recent inspection
Objectives: Damage tolerance assessment using FEA based fracture mechanics studies to evaluate the risk for a continuous operation of another similar unit before next scheduled outage
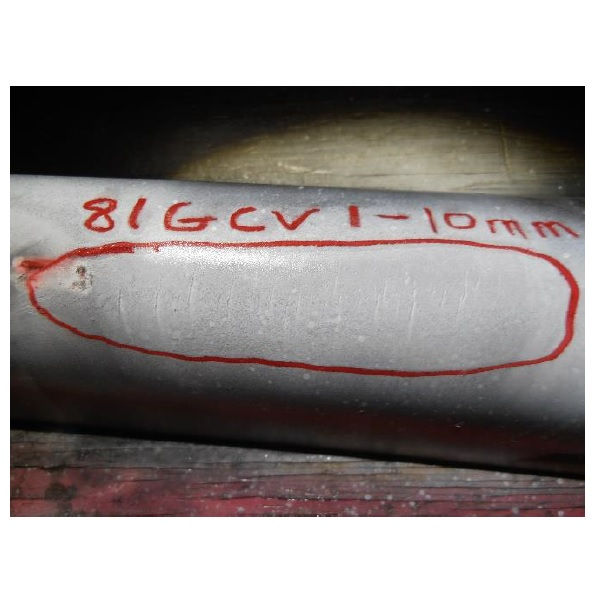

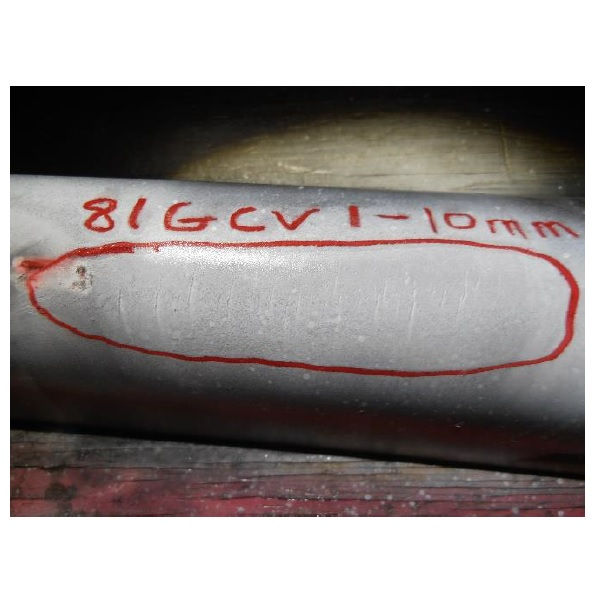
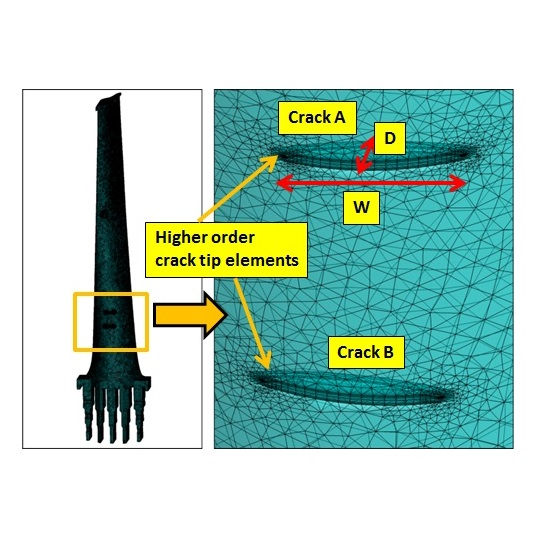


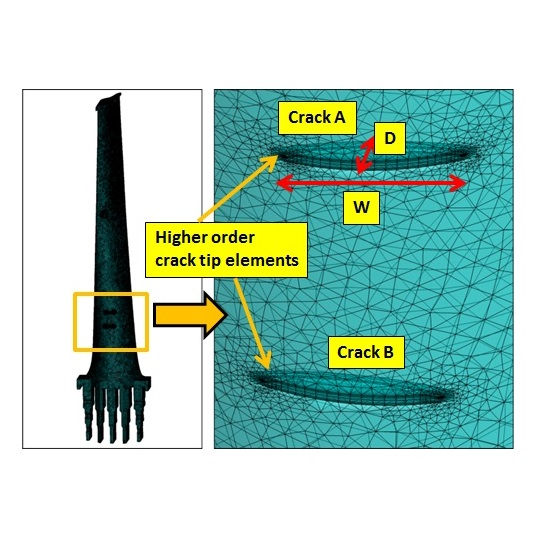
Background
-
Metallurgical analysis indicates that SCC was the driving mechanism behind the observed suction side cracks.
-
Finite element based fracture mechanics studies were carried out to predict the critical crack size and estimation of crack growth rate to assess the risk for a continuous operation of a sister unit.
-
Main objectives of the SCC study include:
1. Calculate stress intensity factor K for various crack sizes and configurations and determine the critical crack limit.
2. Assess the crack growth rate based on the material properties, operating history and field observation.
Summary of Analyses
-
For the largest crack, the calculated stress intensity factor K was well below the nominal fracture toughness of the blade material. The existing cracks appear not to pose an imminent threat of a unstable fracture of the airfoil.
-
Crack growth by HCF is primary mechanism dictating the assessment of critical crack size.
-
A conservative upper bound of crack growth rate was assumed to assess the risk of a continuous operation. It appears that a comfortable margin to the HCF threshold intensity Kth remains before the next scheduled outage.
-
The risk of an airfoil liberation during operation before next inspection is considered to be low for another similar unit.