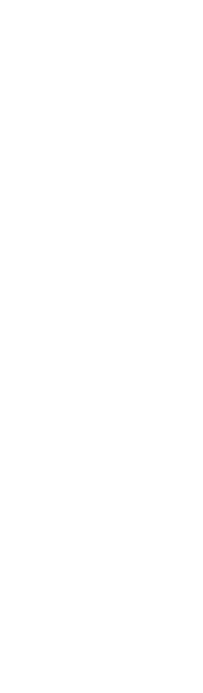
Case study: Detuning and Re-design of Steam Turbine Blades
Stage: Stage 15 and 16 in a steam turbine with an earlier design
Issue: Crack and rupture found at the first hook of straddle mounted root
Objectives: Root cause analysis and blade re-design
Diagnosis: High cycle fatigue (HCF) due to resonance of synchronous vibration was identified as the driver
Solutions: Modification of airfoil profile guided by analysis to de-tune the frequency
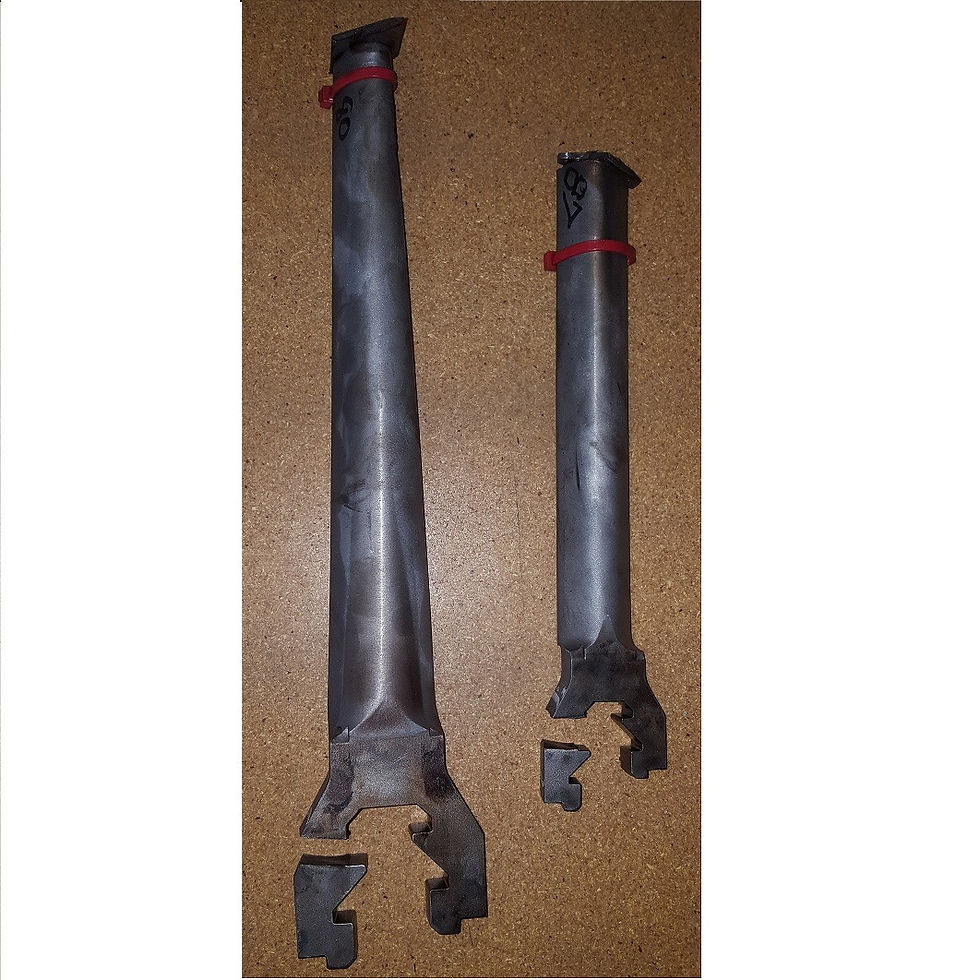
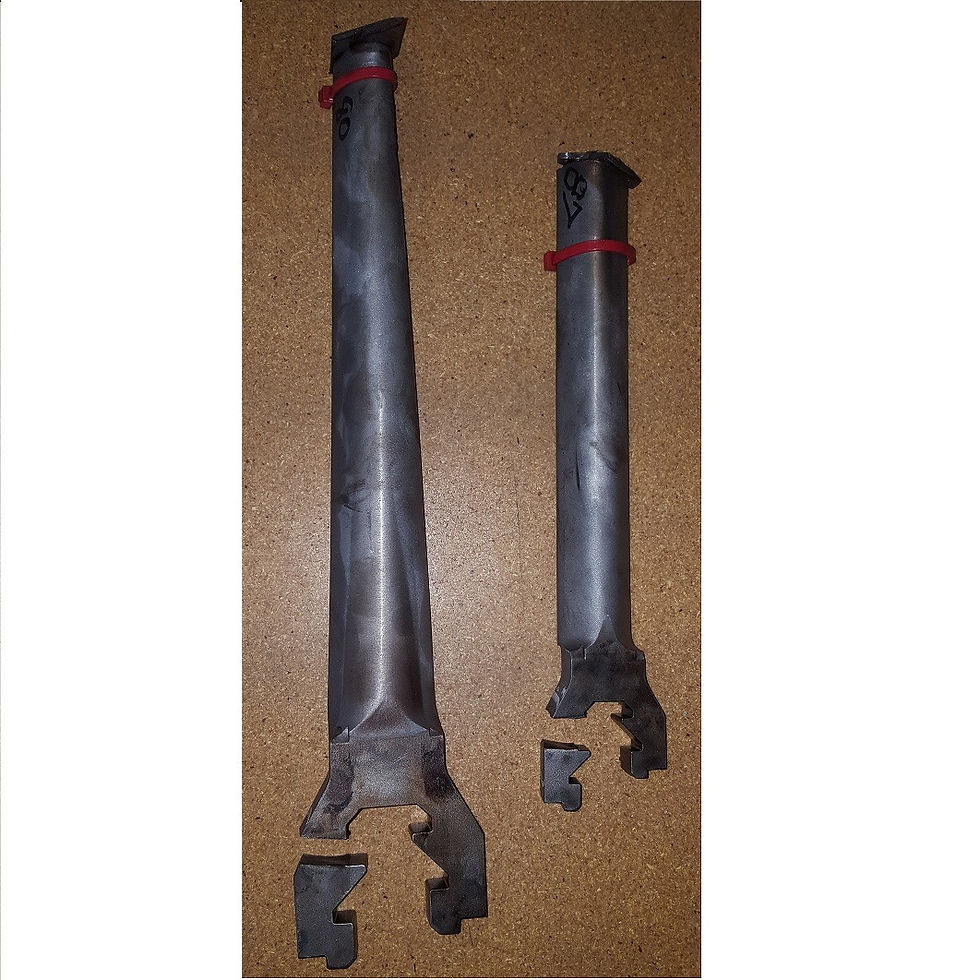
Background
-
Cracks and rupture were found at the first hook of straddle mounted root after a relative short period of time in service.
-
TTI was solicited to perform modal analyses and identify potential resonant modes of vibration.
-
The main objective of the study was to evaluate various de-tuning strategies and optimize configurations to mitigate the resonance issue for both stages.
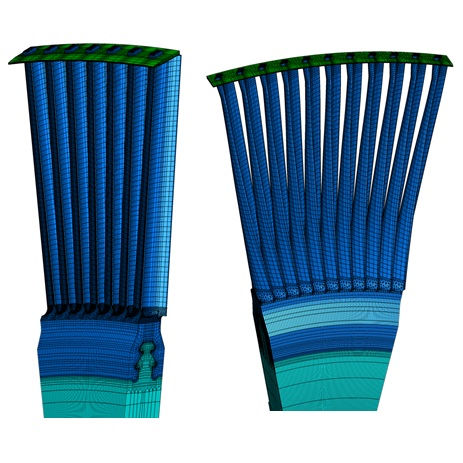


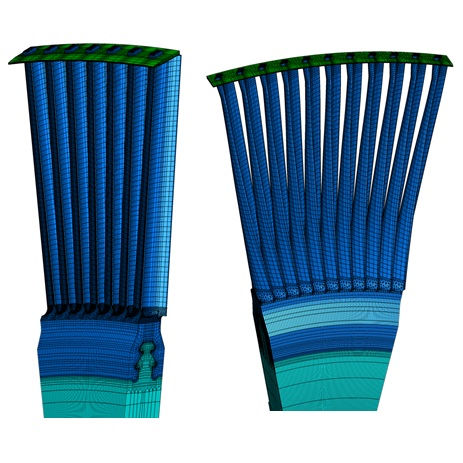
Summary of Analyses
-
At-speed frequencies and mode shapes of the bladed-disk structure were calculated by FEA analysis. Interference diagrams were established to identify potential resonant modes.
-
Several options of de-tuning strategies including re-profiling airfoil, re-grouping and use of different shroud material were examined.
-
Parametric studies were performed to achieve an acceptable solution in regards to margins to the resonant frequencies and level of steady stresses.
-
Increase of fillet radii was also studied to prolong fatigue life.
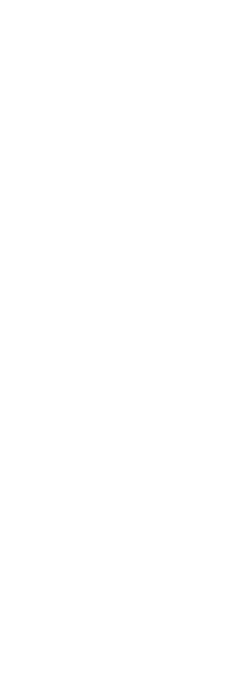