Case study: Flow and Particle Trace Analysis of Erosion at Control Valve Seat
Location: Steam turbine inlet valve
Issue: Severe erosion found at the control valve seat on diffuser
Diagnosis: High speed flow carrying particles hitting valve seat which causes erosion when valve is nearly closed
Solution: New valve design verified by analysis to avoid direct flow and particle to attack valve seat

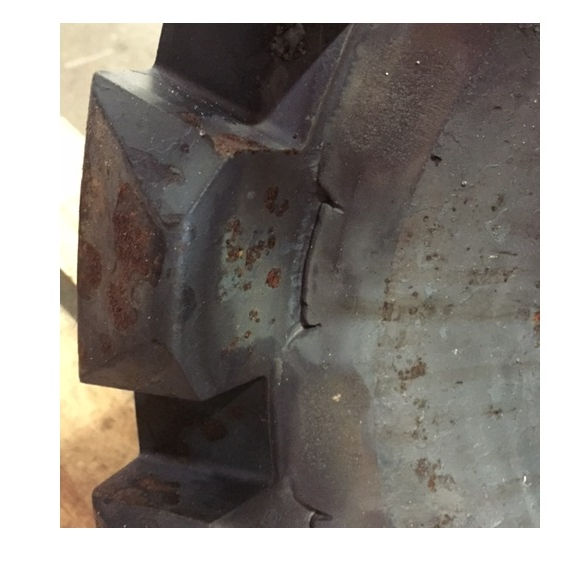
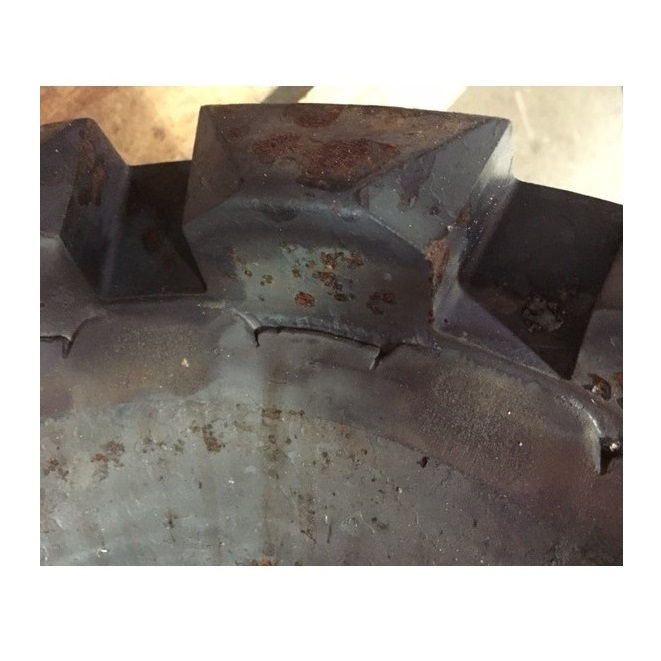





Background
-
Severe erosion was found at control valve seat on diffuser of a steam turbine inlet valve system.
-
TTI was solicited to perform a flow analysis to identify the root cause and verify the new design proposed by third party manufacturer.
Summary of Analyses
-
Results from computational fluid-particle dynamic (CFPD) analysis indicate that the erosion is principally due to extremely high speed flow carrying particles hitting the control valve seat area on diffuser when the control valve is at near closed position (5% opening).
-
The erosion area predicted by CFPD simulation matches the field observation very well.
-
CFPD simulations verify that the new design should be effective in re-distributing the flow and hence significantly reducing the possibility of particle erosion attack.